پیشنیاز های فنی فولاد برای افق ۲۰۲۵
طبق طرح جامع فولاد، ایران باید در سال ۲۰۲۵ به ظرفیت ۵۵ میلیون تنی در تولید فولاد برسد.
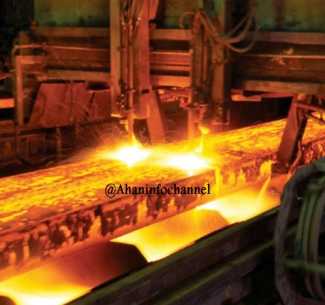
پیشنیازهای فنی فولاد برای افق ۲۰۲۵ طبق طرح جامع فولاد، ایران باید در سال ۲۰۲۵ به ظرفیت ۵۵ میلیون تنی در تولید فولاد برسد. گفته می شود، اجرای طرح جامع فولاد خواسته و هدف نهایی تمامی ارکان بخشهای دولتی و خصوصی ایران به شمار می رود و هیچ چیز حتی تحریم ها قادر نیست ایران را از این هدف دور کند. هدف ایران این است که در بخش معدن به ویژه در اکتشاف، استخراج، فرآوری و کنسانتره سازی سرمایهگذاری های بیش تری را برای جبران کمبود سنگ آهن در سال ۲۰۲۵ انجام دهد. یکی از تحلیل گران بازار های بین المللی فولاد و مواد معدنی طی سخنرانی ای گفت: ایران باید تا این زمان به ظرفیت تولید ۵۵ میلیون تن فولاد دست یابد که در این راستا گلوگاه اصلی تولید سنگ آهن می باشد؛ چرا که در افق ۲۰۲۵ هنوز نیازمند ۱۶۲ میلیون تن سنگ آهن هستیم؛ بر همین اساس، بیش ترین سرمایه گذاری ها باید در بخش اکتشاف، استخراج و فرآوری سنگ آهن انجام گیرد و باید به دنبال جذب سرمایه گذاری در این حوزه بود. صادرات حداقل ۵/ ۱۰ میلیون تن و حداکثر ۲۰ میلیون تن هم اکنون هدف گذاری شده و به نظر میرسد رقم ۵/ ۱۵ میلیون تن واقعی تر بوده و به شرط عدم اعمال تحریم ها دست یافتنی می باشد.
علاوه بر این، صادرات فولاد ایران که در ۵ ماهه اولیه سال مورد بررسی قرار گرفت نشان داد که در ۵ ماهه اول امسال صادرات کل فولاد ایران ۳ میلیون و ۱۰۷ هزار تن بود که نسبت به دوره مشابه سال قبل ۵ درصد افزایش یافته است.
آمار مرداد هم نشان دهنده این است که حجم صادرات که ۴۸۳ هزار و ۵۱۰ تن بوده نسبت به تیر امسال افت ۲۴ درصدی داشت که متاثر از شروع مرحله اول تحریم های آمریکا علیه ایران بوده است. وی در ادامه به تشریح مسایل مربوط به صادرات پرداخت و گفت: فولاد خوزستان بهعنوان برترین صادر کننده فولاد در ایران در مدت مذکور یک میلیون و ۱۱۰ هزار و ۴۶۶ تن فولاد صادر کرد. در این مدت فولاد مبارکه نیز موفق به صادرات ۶۰۲ هزار و ۷۵ تن، ذوب آهن اصفهان ۴۶۳ هزار و ۷۶ تن، فولاد کاوه جنوب ۴۰۵ هزار تن، فولاد هرمزگان ۳۷۳ هزار و ۵۴۹ تن، فولاد خراسان ۱۰۷ هزار و ۴۴۵ تن، فولاد آلیاژی ایران ۳۲ هزار و ۲۲۰ تن و فولاد اکسین ۱۳ هزار و ۳۴۰ تن دست پیدا کردند. جعفری طهرانی در مورد وضعیت تولید آهن اسفنجی، بیلت، بلوم و اسلب گفت: ایران دومین تولید کننده برتر آهن اسفنجی جهان است که در این مدت با رشد ۱۴ درصدی به تولید ۸ میلیون و ۹۸۴ هزار و ۱۴۷ تن تولید رسیده است. برترین تولید کنندگان آهن اسفنجی ایران نیز شامل فولاد مبارکه، فولاد خوزستان، فولاد هرمزگان، فولاد کاوه جنوب و فولاد خراسان هستند.
در رابطه با تولید اسلب و بلوم و بیلت هم باید گفت: تولید اسلب در ۵ ماه اول امسال ۱۷درصد رشد داشته و بزرگ ترین تولید کنندگان امسال به ترتیب فولاد مبارکه، فولاد هرمزگان، فولاد صبا و فولاد خوزستان هستند. همچنین در حوزه بلوم و بیلت تولید ۳ میلیون و ۱۸۷ هزار و ۸۰۰ تن گزارش شده که نسبت به سال گذشته رشد ۱۴ درصدی مشاهده میشود. برترین تولیدکننده بلوم و بیلت در سال قبل فولاد خوزستان بوده است و ذوبآهن اصفهان، فولاد کاوه جنوب کیش، فولاد خراسان و شرکت صنعتی ومعدنی چادرملو در جایگاه های بعدی قرار دارند. این درحالی است که امسال ترتیب در رتبه های اول و دوم به شکل دیگری است و ذوب آهن در رتبه اول و فولاد خوزستان در مقام دوم قرار دارند. این تحلیلگر بازار های بین المللی فولاد و مواد معدنی درباره تاثیر تحریمهای آمریکا بر تولید و صادرات فولاد ایران اظهار کرد: تاثیر این تحریمها بر تولید و صادرات فولاد ایران را نمیتوان نادیده گرفت. تولیدکنندگان و صادرکنندگان به دنبال بازارهای هدف جدید هستند تا بتوانند محصولات خود را با قیمتهای رقابتی به این مناطق صادر کنند. ایران امیدوار است که در دوره تحریم در کنار بهرهگیری از تکنولوژیهای چینی، همچنان شانس استفاده از تکنولوژیهای اروپایی را نیز داشته باشد. همچنین ایران به دنبال همکاری و مشارکت با طرفها و شرکتهای اروپایی و چینی برای سرمایهگذاری مشترک در زمینه ساخت قطعات فنی صنایع فولادسازی در داخل ایران و انتقال دانش فنی ساخت این قطعات در کشور است تا به این شیوه از فولادسازان داخلی در دوره تحریم حمایت کنند.وی تصریح کرد: مشکل اصلی که همه با آن مواجه هستند افزایش قیمت حمل دریایی از بنادر ایران به سایر نقاط و بالعکس و همینطور کمبود کانتینر است. این مساله سبب بروز نگرانیهایی در میان تجار و تولیدکنندگان شده، چراکه با دور جدید تحریمها این مساله ممکن است تشدید شود. پیشرفتهای تکنولوژیک در حوزه فولاد جعفری طهرانی در بخش دیگر سخنرانی خود درخصوص تکنولوژیهای جدید تولید فولاد در ایران گفت: دو پروژه جدید که در زمینه استفاده از تکنولوژیهای نوین و به روز در صنعت فولاد ایران و بر اساس تکنولوژی شرکت Primetals اجرا شدهاند، خطوط تولید محصولات فولادی ESP (Endless Strip Production برای تولید محصولات تخت و ورق و وین لینک برای تولید محصولات طویل به ویژه آرماتور هستند. در هر دو این روشها بهجای رسیدن به محصولات میانی از جمله اسلب و بیلت، ریخته گری درجا انجام میشود و مستقیما به ترتیب به ورق و میلگرد بهعنوان محصولات نهایی در ESP و وین لینک میرسیم بنابراین انرژی مصرفی برای شکل دهی کاهش مییابد و شمش ریخته گری شده بدون سرد شدن وارد خط نورد میشود.
ویژگی ESP، انعطاف پذیری و پاسخگویی سریع به نیازهای بازار، به حداقل رسیدن هزینههای سرمایهگذاری Capex و بهرهبرداری Opex، انطباق بیشتر با مسائل ایمنی و زیست محیطی به علت پرت انرژی کمتر و اشغال فضای بسیار کمتر از خطوط تولید سنتی است؛ بهطوریکه برای یک کارخانه با ظرفیت ۳/ ۲ میلیون تن در سال فقط ۲۰ هزار متر مربع فضا نیاز است در صورتیکه در روشهای ریختهگری سنتی با ظرفیت بین ۸/ ۲ الی ۴ میلیون تن در سال بین ۶۰ هزار تا ۱۰۰ هزار متر مربع یعنی ۳ الی ۵ برابر فضای بیشتر مورد نیاز است.
درمورد وین لینک نیز همچنین هزینههای بهرهبرداری و عملیاتی کاهش چشمگیری نسبت به روشهای سنتی دارد. شاخصهای زیستمحیطی نظیر مصرف انرژی نیز در «وین لینک» به واسطه احتراق کمتر، کاهش قابل ملاحظهای دارد. کما اینکه به زمین کمتری نیاز داریم و این کاهش فضای اشغالی نسبت به محصولات طویل نسلهای قبل به حدود ۴۰ درصد میرسد. در بخش تجهیزات و احجام سازه و سیویل هر کدام ۲۰ درصد و در حوزه زیرساخت ۳۰ درصد افت را شاهد خواهیم بود. در بخش مصرف گاز ۷۰ درصد، نیروی انسانی ۴۰ درصد، پرت و دور ریز متریال ۸۰ درصد و نهایتا در مصرف انرژی ۲۰ درصد کاهش خواهیم داشت. براساس طرح جامع فولاد و توسعه صنعت فولاد ایران، این تکنولوژیهای نوین که از سوی شرکت «پری متالز» ارائه شدهاند هماکنون در طرح توسعه آهن و فولاد گل گهر به ظرفیت ۳میلیون تن برای تولید ورق به روش ESP و نیز مجتمع فولاد روهینا جنوب به ظرفیت ۴۵۰ هزار تن آرماتور به روش وین لینک اجرا شدهاند و در حال بهرهبرداری میباشند. آب و پیشرفتهای فولادی برای بهینهسازی وی در بخش دیگری از سخنرانی خود به موضوع بهینهسازی خنککنندههای آبی در پروژههای فولادی و اقداماتی که در طرح جامع فولاد به این منظور توصیه شده پرداخت؛ چراکه ایران سرزمینی خشک محسوب شده و با چالش آب مواجه است. جعفری طهرانی گفت: بهطور کلی عمده مصرف آب در صنعت فولاد مربوط به سیستمهای خنککننده و برجهای خنککننده است. در برجهای خنککننده تلفات آب به سه صورت اتفاق میافتد. اول تبخیر آب که موجب اتلاف بخشی از آب و خنک شدن مابقی آبهای باقیمانده میشود. دوم پرتاب قطرات آب توسط پروانه کولینگها به اتمسفر انجام میشود و سوم مقدار آبی است که توسط بلودان در سیکل خنککننده به منظور کنترل آب چرخشی، تخلیه و ته کشی میشود. در غیر این صورت املاح موجود در آب به حدی میرسد که میتواند موجب آسیب رسیدن به تجهیزات شود. لذا بخشی از آب حتما باید با عنوان بلودان تخلیه شود.
جعفری طهرانی تصریح کرد: برای کاهش مصارف آب میتوان از برجهای خنککننده هیبریدی استفاده کرد که در این برجها بهجای استفاده تنها از انتقال حرارت یا تبخیر پنهان از انتقال حرارت ناشی از اختلاف دمای آب گردشی و دمای محیط بهصورت محسوس نیز استفاده میشود. این امر سبب میشود بخشی از تبخیر آب که در راستای خنک کنندگی انجام میشده جایگزین شود با انتقال حرارتی که بهصورت محسوس انجام میشود و به این ترتیب بخشی از اتلاف آب از طریق تبخیر، کاهش مییابد. راهکار دوم این است که برج خنککننده را از نوع آبی به یک برج خنککننده هوایی نظیر رادیاتورهای هوای خنک تبدیل کنیم، البته این موضوع درصورتی امکان پذیر است که اختلاف سطح دمای آب رفت و برگشت برج خنککننده و تجهیزات تکنولوژیک را بتوان بالا برد تا بتوان از دمای محیط برای خنک کردن آب استفاده کرد.این روش مشابه رادیاتور اتومبیل عمل خواهد کرد. در این روش اگر سطح دمای رفت و برگشت را بالاتر ببریم؛ مثلا ۶۰درجه دمای آبی باشد که به سیستم خنککننده وارد میشود و ۵۰درجه دمای آبی باشد که بر میگردد، در این صورت اختلاف دمای آبی که میخواهیم خنک کنیم با دمای محیط به حدی میرسد که میتوانیم از دمای محیط برای خنک کردن آن استفاده کنیم. با بهکارگیری این روش یا رادیاتورهای هوای خنک عملا برج خنککننده آبی حذف شده و هر سه نوع اتلاف آب به حداقل کاهش مییابد.وی در ادامه مباحث، اشارهای به تجاربی که در کاهش مصرف آب در پروژههای اجرا شده در ایران بوده داشت و اظهار کرد: این تجارب نشان میدهد در روشهایی که هوا جایگزین آب در برجهای خنککننده شده مصرف آب بهطور چشمگیری کاهش یافته است. البته استفاده از این روش مدرن منوط به این مساله است که تجهیزات فولادی قابلیت کار در دماهای بالاتر را پیدا کنند و این موضوع به کیفیت مواد مورد استفاده در ساخت تجهیزات و قطعات بستگی دارد. در ریختهگری شماره ۵ فولاد مبارکه به ظرفیت ۲ میلیون تن در سال، برای خنک کردن آب از برجهای هیبریدی استفاده شده که موجب کاهش اتلاف آب از ۱۲۵ مترمکعب بر ساعت به ۱۰۰ مترمکعب بر ساعت شده یا به عبارتی حدود ۲۰ درصد کاهش یافته است.
در پروژه فولاد نیریز که جزو پروژههای استانی به ظرفیت ۸۰۰ هزار تن در سال است، مصرف آب ۳۲۹ مترمکعب بر ساعت بوده است. شرکت بینالمللی فولاد تکنیک که بهصورت EPC پروژه اخیر بر عهدهاش بوده توانسته با بهکارگیری سیستم خنککننده که درتکنولوژیهای Fume Treatment Plant و Electrical Arc Furnace و Ladder Furnace استفاده شده و همچنین بهکارگیری Air Cooler و بالا بردن دمای رفت و برگشت آب، میزان مصرف آب را به ۱۱۸ مترمکعب بر ساعت کاهش دهد. در فولاد نیریز علاوه بر این اقدام، کیفیت آب نیز ارتقا یافت تا شاهد کاهش مصرف و اتلاف آب دورریز یا Blow Down باشیم که این موضوع سبب شد مصرف آب در این پروژه به ۱۰۵مترمکعب بر ساعت کاهش یابد و این یعنی ۶۸ درصد کاهش در مصرف آب. استفاده از خنککنندههای هوایی به رغم نقاط قوت زیادی که دارند دو نقطه ضعف دارند و آن افزایش مصرف برق به جهت استفاده از فن و الکتروموتورها در آن است و این افزایش مصرف برق به ۱۸۰۰ کیلووات ساعت میرسد. همچنین حجم سرمایهگذاری مورد نیاز در اینگونه پروژهها بالاست و در پروژه فولادسازی نیریز ۴ میلیون یورو افزایش هزینه داشتیم و درمقابل شاهد کاهش مصرف چشمگیری در آب بودیم. در طرح جامع فولاد نیز بهرهگیری از این روشها توصیه شده است بنابراین در میان این دو تکنولوژی نیز استفاده از روش Air Cooler مناسبتر است. وی به مساله اتوماسیون در واحدهای احیای مستقیم ایران پرداخت و گفت: اگرچه برخی معتقدند انقلاب صنعتی چهارم یا Industry ۴ خیلی بالاتر از سطح ۲ اتوماسیون است اما مقایسه سطح ۲ اتوماسیون با صنعت چهارم یا Industry ۴ یک اشتباه فاحش است.
در واقع Industry ۴ یک زیرساخت اطلاعاتی در یک کارخانه و پیشنیازی برای انجام اتوماسیون سطح ۲ است. به عبارت دیگر پس از برقراری ارتباط اطلاعاتی میان سنسورها، سیستمهای کنترل و سایر تجهیزات مکانیکی و از طریق یک فرآیند بر اساس تکنولوژیهای مختلف از جمله Internet of Things یا IOT، میتوان صحبت از مدلسازی فرآیند و بهینهسازی کرد. وقتی اتوماسیون سطح ۲ را انجام میدهیم به این معناست که قبل از آن، وارد Industry ۴ شدهایم و به سطوح بالای آن رسیدهایم. وی از جمله مزایای سطح ۲ اتوماسیون را افزایش بازدهی، کاهش زمانهای خاموشی کارخانه، کاهش مصرف انرژی و حفاظت از مسائل زیست محیطی دانست و ادامه داد: شرکت فولاد تکنیک بهعنوان پیشرو اتوماسیون صنعتی در صنایع آهن و فولاد ایران به موازات کلیه شرکتهای پیشرو دنیا روی این سناریو بهصورت آزمایشی و پایلوت در دو کارخانه احیای مستقیم کار میکند و با بهرهگیری از هوش مصنوعی و شبکه عصبی، نتایج بسیار خوبی نیز اخذ کرده است. کنترل و مدیریت از راه دور کارخانههای صنعتی برای راهاندازی کارخانههای فولاد نیاز است که از ابتدای راهاندازی و شروع بهرهبرداری از کارخانه به ویژه ظرف یک سال اول، تمامی شرایط و کلیه روند کارخانه مورد مشاهده و کنترل قرار گیرد و این مقدور نخواهد بود مگر از طریق کنترل از راه دور از دفتر مرکزی. کنترل از راه دور نیز نیازمند پیششرطهایی است که شامل ایجاد زیربنا و مقدمات ارتباط میان کارخانه و دفتر مرکزی بوده و نیازمند یک شبکه امن و سریع میان این دو است. بنابراین سیستم مدیریت از راه دور با استفاده از شبکههای ایمنی در سطوح متعددی در کارخانههای صنعتی زیادی در ایران اجرایی شده است.
جعفریطهرانی ادامه داد: در بخش تعمیر و نگهداری «پیشبینی شده و پیشگیریکننده» باید گفت همزمان با راهاندازی کارخانه نیاز است که تعمیر و نگهداری انجام شود و بناست که در هر کارخانه تعدادی از تکنسینها با توجه به شرایط کار و مکانیزم کارخانه، الگوریتم پیشگیری هر یک از عوامل مهم شامل آنالیز ارزش، صدا و حرارت و نیز آنالیز مکانیزم جریان الکتریکی را بررسی کنند؛ چراکه شناسایی این عوامل سبب میشود تا احتمال توقف کاری و تعمیر هر یک از بخشهای کارخانه مشخص شود. این اقدام در تجهیزات بزرگی نظیر کمپرسورها و دمندهها سبب میشود احتمال توقفات متعدد بررسی و از توقفات طولانی جلوگیری شود. این امکان نیز در مراحل مقدماتی بوده و برای فولادسازان کشور ارائه شده است. همچنین بر اساس اطلاعاتی که از مرحله تعمیر و نگهداری پیشگیریکننده به دست آمد، میتوان شناسایی کرد که در کدام قسمت کارخانه ممکن است آسیبی ایجاد شود یا در اثر موردی که در مرحله پیشبینیشده شناسایی شده چه آسیبی به سایر بخشها خواهد رسید تا جلوی آن گرفته شود و این مورد نیز اجرایی شده است. گرداوری شده توسط آهن اینفو 21 مهر 97 منبع: دنیای معدن