نورد سرد چیست؟ مزایا و فرایندهای آن
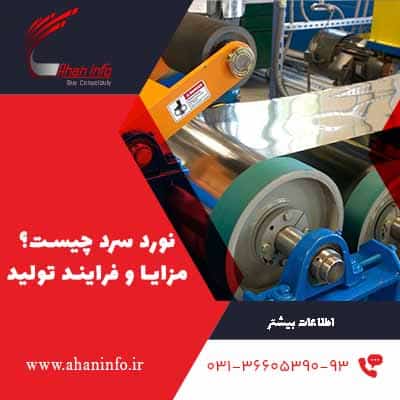
ورق های فولادی طی فرآیندهای نورد سرد (cold rolling) و گرم (hot rolling) به انواع محصولات فولادی تبدیل می شوند. در واقع فرآیند نورد سرد یکی از اصلی ترین عملیات ها در جهت تولید ورق های فولادی به شمار می آید؛ زیرا بدون حرارت و با استفاده از اعمال فشار بسیار زیاد در دمای زیر تبلور بر روی ورق های اسیدشویی شده صورت می گیرد. این فرآیند شامل عملیات های متعددی بوده که از جمله مهم ترین آن ها می توان به شستشوی الکترولیتی، نورد سرد، آنیلینگ، پاشش آب و روغن، لبه بری و پرداخت سطحی اشاره کرد.
این فرایند بر خلاف نورد
گرم، در دمای پایین اما با فشار بالا انجام می شود. فلز به تدریج فشرده می شود و
قدرت تسلیم و سختی آن افزایش پیدا می کند. هدف از این نورد، تولید ورق هایی نازک
با دقت ابعادی و کیفیت سطحی مناسب می باشد. محصول نهایی به دست آمده از این روش،
دارای ساختار مقاوم تر، پرداخت یک نواخت و فاقد خلل و فرج می باشد. با این حال،
محصولات هنگامی که در دمای بالا پردازش می شوند، استحکام بیشتری در مقابل خوردگی
به دست می آورند.
مراحل انجام نورد سرد
ورق های فولادی پس از طی
کردن مرحله نورد گرم، به ورق سیاه تبدیل می شوند، اما این محصول به سبب طی کردن فرآیند
نورد گرم و دمای بسیار بالا، دارای سطحی زبر و دارای پوسته های اکسیدی می باشد؛ از
این رو باید ابتدا اسیدشویی شود و سپس تحت فرآیند نورد سرد قرار بگیرد. زیرا این
سطح زبر ممکن است به غلتک های نورد آسیب برساند. حال مراحل انجام نورد سرد در
ادامه شرح داده شده اند تا درک بهتری از انجام این عملیات ها داشته باشید:
1-ابتدایی ترین مرحله برای تولید ورق های سرد که
نام دیگر آن ها ورق روغنی نیز می باشد، اسیدشویی نامیده می شود. این فرآیند در
دمای 50 تا 85 درجه سانتی گراد با غوطه وری ورق های سیاه در مخازن اسید صورت گرفته
و زمان آن بسته به غلظت اسید مورد استفاده و سایر شرایط محیطی در حد 20 ثانیه تا 5
دقیقه طول می کشد. در واقع دلیل مقاومت بیشتر ورق های سرد به علت فرایند نورد سرد
و افزایش مقاومت سطحی آن می باشد. کیفیت ظاهری بهتر این محصول نیز نسبت به ورق
سیاه موجب استفاده از آن در صنایع مهمی مانند خودروسازی و لوازم خانگی و مورد
اهمیت قرار گرفتن قیمت امروز ورق روغنی برای تولیدکنندگان این صنایع شده است. در واقع
یکی از دلایل کیفیت ظاهری بالا برای این فلزات، مربوط به نحوه انجام فرآیند
اسیدشویی و پاکسازی سطح ورق های اولیه است.
2-در
مرحله بعدی برای از بین بردن باقی مانده لایه های اسیدی، شستشوی آبشاری ورق های
فولادی انجام می گیرد. در پایان این مرحله نیز شیت ها به خوبی خشک می گردند.
3-بخش
بعدی شامل انجام اصلی ترین مرحله یعنی نورد سرد است. روش انجام آن نیز به صورتی
است که پس از انجام فرایند نورد گرم، مرحله خنک شدن فولاد به اندازه دمای فضا باید
طی شود. سپس غلتک های دستگاه نورد سرد در دمایی پایین تر از تلبور از روی آن ها
عبور می کند تا به ضخامت مورد نظر برسند.
4-این
غلتک ها با عبور رفت و برگشتی از روی شیت ها سبب کاهش ضخامت آن ها تا میزان مورد
نظر خواهند شد، اما باید در نظر داشته باشید، ممکن است آلودگی هایی را بر سطح شیت
ها باقی بگزارند؛ به همین علت در این بخش با استفاده از محلول های یونیزاسیون، سطح
آن ها را به روش الکترولیتی مجدداً شستشو می دهند. در پایان این بخش نیز شیت ها
خشک شده و به رول تبدیل می شوند. محصول نهایی این بخش ورق سرد یا فول هارد نام
دارد.
5-لازم
به ذکر است عملیات رفت و برگشتی غلتک ها به طور معمول باعث کاهش ضخامت 50 تا 90
درصد خواهد شد. همچنین به دلیل وجود نیروهای فشاری و اصطحکاک بالا، امکان رسیدن
دمای هر دور به 250 درجه سانتی گراد، فراهم می باشد؛ در نتیجه برای سرد نگه داشتن
غلتک ها به یک سیستم خنک کننده نیاز است. این سیستم خنک کننده به وسیله روغن یا آب
صورت می گیرد.
6-این
مرحله بسیار حائز اهمیت بوده و تعیین کننده خواص و کیفیت ورق سرد نهایی می باشد.
به این ترتیب رول های فولادی فول هارد وارد یک سری کوره آنیلینگ یا بازپخت شده که
دمایی در حدود 800 درجه سانتی گراد داشته و از اتمسفر هیدروژنی اشباع شده اند. این
عملیات در حدود 5 تا 20 دقیقه به طول می انجامد و سبب بهبود خواص مکانیکی و استانداردهای
تولید گرید محصول خواهد شد.
7-حال
در این بخش رول های فولادی کمی توسط روش های مخصوص خنک شده و مجدداً به شیت تبدیل
می شوند؛ زیرا حرارت کوره های آنیل ممکن است موج یا تاب هایی را در رول ها به وجود
آورده باشد؛ از این رو باید دوباره شیت ها از نورد دو مرحله ای با استفاده از
دستگاه تمپر رولینگ عبور کنند تا سطح آن ها صافی مورد نظر را به دست آورد.
8-پس
از رسیدن شیت ها به سطح مد نظر، لایه پوششی مانند روغن در جهت محافظت از سطح آن ها
در برابر عوامل خوردگی و زنگ زدگی بر روی آن ها اعمال می گردد.
9-بخش بعدی شامل لبه بری شیت های روغنی و تبدیل آن ها به رول یا شیت های فابریک مطابق با تولید و عرضه کارخانه است.
حتما بخوانید:کاربرد ورق روغنی
دستگاه ها و ماشین های نورد سرد
این فرایند با استفاده
از دستگاه هایی همراه با تجهیزات پیشرفته انجام می شود. از دستگاه های به روز و
مطابق با تکنولوژی روز جهت انجام فرایند های مختلفی استفاده می شود. البته لازم به
ذکر است برخی از آن ها فقط برای تولید یک مقطع فولادی کاربرد دارند و به نوعی تک
منظوره هستند. اغلب دستگاه ها و ماشین آلات جهت ساخت مقاطعی با ابعاد و ضخامت مشخص
مورد استفاده قرار می گیرند.
هر چه دستگاه بزرگ تر
باشد، نتیجه نهایی ابعاد بیشتری دارد. نصب و نگهداری آن ها راحت و به صرفه می
باشد؛ در نتیجه نیازی به تعمیر و نگهداری بیش از حد ندارند. این دستگاه ها قادر به
کنترل کردن سرعت چرخش، میزان درز و جهت رفت و برگشت غلتک ها می باشند.
با این وجود می توان گفت
دستگاه نورد سرد دارای قابلیت تنظیم سرعت چرخش غلتک ها بر روی ورق های فولادی
بوده؛ به طوری که درز بین غلتک ها نیز با فواصل مشخصی تعیین می شوند. اصلی ترین
ویژگی دستگاه های نورد سرد به رفت و برگشتی بودن حرکت غلتک های آن ها باز می گردد؛
در واقع به همین علت ورق های روغنی حاصل از این فرآیند علاوه بر اینکه از خواص مهم
مکانیکی و کیفیت سطحی بالا برخوردار هستند، در تولید سایر ورق های فولادی نیز به
کار می روند. از جمله این محصولات نیز می توان به ورق های گالوانیزه و پوششی اشاره
کرد. در واقع خرید ورق گالوانیزه به افراد و تولیدکنندگانی پیشنهاد می شود که جدا
از سطح ظاهری، میزان مقاومت ورق فولادی در برابر خوردگی و زنگ زدگی برای آن ها
حائز اهمیت است.
انواع آسیاب نورد سرد
به صورت کلی آسیاب های
دستگاه نورد سرد شامل تعداد غلتک های مختلفی هستند، اما در کل در 5 دسته اصلی
خلاصه می شوند که در ادامه به شرح اختصاری هر کدام پرداخته شده است:
آسیاب دو غلتکی: رایج
ترین شکل آسیاب که از نام آن نیز می توان به ماهیت آن پی برد، آسیاب دو غلتکی نورد
سرد می باشد که دارای دو غلتک با قطرهایی در حدود 6/0 تا 4/1 متر است. این آسیاب
ها قابلیت چرخش معکوس در جهت یک دیگر را دارند.
آسیاب سه غلتکی: این نوع
آسیاب، قابلیتی به نام معکوس سازی غلتک ها ندارد، اما از طرفی دیگر، در آخر هر
مسیر باید با استفاده از بالابر یا ابزار دیگری برای چرخاندن قطعه فولادی استفاده
کرد. فرآیند نورد با استفاده از این آسیاب ها به انرژی کمی نیاز دارد؛ زیرا غلتک
های کوچک سبب ایجاد طول تماس کمتری خواهند شد.
آسیاب چهار غلتکی: در این دستگاه با دو غلتک اصلی و دو غلتک پشتیبان، سبب
کاهش ضخامت ورق فولادی می شوند. این نوع آسیاب هم در فرایند نورد سرد و هم در نورد
گرم کاربرد دارد.
نورد خوشه ای: این نوع
آسیاب نیز مانند نوع چهار غلتکی شامل غلتک های پشتیبان می باشد. همچنین در این
دستگاه ها، غلتکی که با قطعه در تماس است، قطری در حدود 6 میلی متر دارد.
نورد پیوسته: آخرین
آسیابی که به شرح آن می پردازیم، نورد پیوسته نامیده می شود و قابلیت تولید انواع
مقاطع فولادی با اشکال ظاهری مختلف با آن وجود دارد.
مقاطع تولید شده در نورد سرد
پرکاربردترین و محبوب
ترین محصولات تولید شده در فرایند نورد سرد، ورق سرد یا روغنی می باشد که خود به
ورق گالوانیزه، رنگی و قلع اندود تبدیل می شود. این روند بخش ویژه ای از صنعت
تولید محصولات فولادی را به خود اختصاص داده است. دلیل انجام این فرایند، به وجود
آمدن ورق هایی با ضخامت کم و با ابعاد کنترل شده می باشد. از جمله مشخصاتی که
فرایند نورد سرد دارد می توان به افزایش سختی محصول مورد نظر نهایی، ازدیاد تنش
تسلیم و افزایش نابجایی در ساختار کریستالی شیت ها اشاره کرد.
از دیگر محصولات و
مقاطعی که طی فرایند نورد سرد تولید می شوند می توان به تسمه و میلگرد اشاره کرد.
به طور کلی هر قطعه ای که سطح مقطع ثابتی داشته باشد با روش غلتکی نورد سرد قابل
تولید و عرضه می باشد. فایده آن ها در ضخامت کم و مقاومت بیشتر در مقایسه با ورق
های گرم است. از دیگر مقاطعی که از فرآیند نورد سرد به دست می آیند می توان به
موارد زیر اشاره کرد:
- مقاطع باز مانند تیرآهن، سپری، ناودانی و
غیره
- مقاطع عریض مانند انواع ورق
روغنی، گالوانیزه، قلع اندود، فولاد ضد زنگ و ...
- مقاطع بسته مثل انواع قوطی و
لوله ها مانند لوله های استیل
مزیت های نورد سرد
محصولات تولید شده از
نورد سرد به دلیل داشتن مزیت های بسیار، محبوبیت زیادی در بین صنایع پیدا کرده
است. برخی از این مزایا شامل موارد زیر می باشد:
- بر خلاف نورد گرم، محصولات با ابعاد دقیق تولید
می شوند.
- سختی محصولات تولید شده با این روش تا 20 درصد
افزایش خواهد داشت.
- ورق سرد از قابلیت شکل گیری بهره مند می باشد.
- انعطاف پذیری و مقاومت در نورد سرد بالاتر می
باشد.
- محصول تولید شده با روش نورد سرد استحکام بسیار
بالایی دارد.
در نهایت بهتر است
بدانید فرایند تولید نورد سرد با محدودیت هایی نیز همراه می باشد که در این میان
می توان به شکل پذیری ماده و تعداد ایستگاه های دستگاه اشاره کرد. منظور از تعداد
ایستگاه های دستگاه به این علت است که در برخی مواقع باید محصول چند بار از مقاطع
دستگاه رد شود. در صورتی که در برخی اوقات بهتر است از همین روش برای تولید یک
محصول استفاده کرد. در فرایند نورد گرم این محدودیت ها دیگر وجود ندارد، اما محصول
نهایی کیفیت سطح عالی و درخشان و خواص مکانیکی بهبود یافته ای نخواهد داشت. از
طرفی دیگر قیمت ورق گرم مقرون به صرفه از محصولات سرد و روغنی می باشد و همین
موضوع به همراه تنوع کیفیت ها، سبب کاربرد گسترده این فلزات در صنعت شده است.
کاربرد محصولات تولید شده در نورد سرد
فولاد تولید شده توسط
فرایند نورد سرد تحت عنوان یک ماده خام، کاربردهای وسیعی در صنایع مختلف مهندسی
پزشکی، هوا فضا و خودروسازی دارد. بسیاری از این محصولات مانند ورق های روغنی به
صورت مستقیم و غیر مستقیم و با انواع کیفیت سطحی زبر، مات، براق و نیمه براق به دو
صورت رول و شیت تولید می شوند. این موضوع به کاربرد نهایی آن ها باز می گردد. یکی
از برترین تولیدکنندگان این فلزات در کشور ما، شرکت صنایع هفت الماس می باشد؛ از
این رو پیشنهاد می شود برای خرید ورق روغنی هفت الماس ابتدا کاربرد مد نظر خود را
مشخص کنید و با شرکت های تأمین کننده انواع ورق های فولادی در این زمینه مشورت
کرده و سپس سفارش خود را توسط آن ها به کارخانه ثبت کنید. با این وجود از دیگر
کاربرد های ورق های سرد و محصولات حاصل از نورد سرد می توان به موارد زیر اشاره
کرد:
- انواع پروفیل باز و بسته همچون زد، آبرو، قوطی و
پروفیل
- ورق روغنی و به سبب آن ساخت بدنه و تجهیزات لوازم
خانگی، خودروسازی، قفسه سازی و ...
- ورق گالوانیزه و تولید محصولات رنگی و شیروانی،
بدنه و شاسی اتومبیل، بدنه لوازم خانگی، کانال کولر و تهویه، تجهیزات گرمایشی
سرمایشی، پوشش دهی انواع سقف ها، ساندویچ پانل و ...
- ورق های قلع اندود در ساخت و بسته بندی مواد
غذایی
جمع بندی
در پایان باید گفت نورد
سرد یکی از فرایند های مورد استفاده در دمای پایین تر از تبلور می باشد که به صورت
حدودی هم دما با محیط می باشد. مزیت های نورد سرد باعث استفاده از آن در جهت تولید
انواع مقاطع فولادی شده است. با استفاده از نورد سرد محصولاتی مانند پروفیل مقطع
باز و بسته و انواع ورق های فولادی تولید می شوند. ورق های روغنی نیز از این روند
به دست می آیند و کاربرد گسترده ای در صنایع خصوصاً خودرو سازی، قفسه سازی، مبلمان
سازی، لوازم خانگی و مواردی از این قبیل که سطح ظاهری و پرداخت آن حائز اهمیت است،
دارند.