تفاوت کوره القایی و قوس الکتریکی
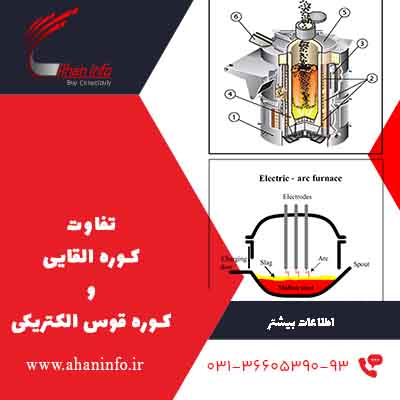
به طور کلی دو روش اصلی برای احیا سنگ آهن و تولید فولاد و محصولات حاصل از آن وجود دارد. این دو روش شامل کوره القایی و کوره قوس الکتریکی است. برای تولید مقاطع و ورق های فولادی نیاز به استخراج سنگ آهن از معادن است. سنگ آهن دارای کانی های مختلف و همچنین اشکال ظاهری متفاوت است، اما باید توجه داشت استفاده از آن به همین شکل امکان پذیر نمی باشد و نیاز به احیا دارد. فرآیند احیا نیز در همین جهت انجام می گردد تا ناخالصی های اضافی سنگ آهن از بین رفته و آهن خام به دست آید.
انجام فرآیند احیا به دو
روش و با استفاده از دو نوع کوره القایی و قوس الکتریکی انجام می گردد. گرمایش
القایی روشی است که در آن موادی که رسانای الکتریکی دارند، گرم می شوند و از راه
القای الکترومغناطیسی انجام می گیرد. به نوعی دیگر می توان گفت تغییرات شار
مغناطیسی حاصل از جریان متناوب همراه با فرکانس بالا در یک رسانا ، سبب القا شدن
گرمایش می گردد. این نوع جریان گردابی نامیده می شود که در کوره قوس الکتریکی با
استفاده از یک ترانسفوماتور انجام می شود.
امروزه
تمامی مقاطع فولادی با استفاده از این دو روش تولید می شوند؛ از سوی دیگر نیز هر
تولید کننده به دنبال تولید فولاد با هزینه کمتر و کیفیت بهتری است؛ در نتیجه هر
کوره مزایا و معایبی دارد که برای آن ها در کیفیت نهایی حائز اهمیت است. در ادامه
مطلب ابتدا به معرفی کوره های قوس الکتریکی
و القایی و در نهایت مقایسه آن ها می پردازیم. با این وجود بهتر است بدانید
این دو روش در نحوه ذوب، ظرفیت تولید، آسیب های زیست محیطی، سایز، توانایی تصفیه
در مقدار کربن و بازده ترمودینامیکی و جنبشی با دیگر تفاوت دارند.
در
کوره های القایی برای ذوب، از جریان القا استفاده شده و کربن در آن افزایش نمی یابد،
در صورتی که کوره قوس الکتریکی برای ذوب مواد از الکترود گرافیت استفاده می کند؛
در نتیجه این الکترود مصرف شده و سبب افزایش کربن خواهد شد. این اصلی ترین تفاوت
کوره های القایی و قوس است.
تولید فولاد و نحوه کار کوره القایی
همان طور که پیش تر نیز
اشاره شد، کوره القایی در واقع یک کوره الکتریکی است که از طریق رسانای مواد
الکتریکی و القا شدن آن ها، گرما تولید می کند. از مزیت های استفاده از کوره های
القایی می توان به سرعت تولید، ذوب تمیز و صرفه جویی در مصرف اشاره کرد. نحوه کار
این روش به صورتی است که ولتاژ بالا در کویل اصلی، سبب القای ولتاژ پایین و جریان
بالا در قراضه های آهن خواهد شد. این سیستم نوعی کویل ثانویه است و در آن انرژی
حاصل به گرما تبدیل می شود و این موضوع نیز به علت رسانایی و مقاومت الکتریکی فلز
است.
با استفاده از گرما و
حرارت، فلز ذوب شده و تا اتمام کار، میدان مغناطیسی موجود، سبب به وجود آمدن خاصیت
همزنی شده و در نهایت توان و فرکانس اعمالی این میزان را مشخص می کند. بهتر است
بدانید احیا سنگ آهن با استفاده از این روش در کشور ما بسیار کم به کار برده می
شود و حدود 90 درصد از صنایع، به کاربردن کوره قوس الکتریکی را ترجیح داده اند. با
این وجود می توان گفت قیمت آهن بسته به این که کارخانه فولادسازی از چه روشی
استفاده می کند، متفاوت است. هر چه روش مورد استفاده برای احیا، کیفیت مواد مذاب،
آنالیز شیمیایی آن، مقادیر عناصر به کار رفته و ... در آن کیفیت بالاتری داشته
باشند، طبیعتاً نرخ آهن نیز بیشتر خواهد شد.
فرآیند تولید فولاد با استفاده از کوره قوس الکتریکی (Electric Arc Furnace)
کوره قوس الکتریکی نیز
یک محفظه بسیار داغ و بسته است که برای تولید فولاد در آن، حرارت با استفاده از یک
سری الکترود و جریان تأمین می شود. قوس الکتریکی که بین الکترود ها و قراضه آهن به
همراه آهن اسفنجی و مواد اضافی ایجاد می شود، بدون از بین رفتن خواص الکتروشیمیایی
ماده سبب ذوب کردن ضایعات مورد استفاده خواهد شد. امروزه حدود یک چهارم فولاد جهان
به وسیله این روش تولید می شود. همچنین در کشور ما از این روش بیشتر استفاده شده و
در نتیجه قیمت ورق سیاه بر اساس فولادسازی به این روش برآورد می شود؛ زیرا فولاد
خام برای تولید اسلب و سپس ورق سیاه به واحد نورد گرم منتقل می شود. در واقع
آنالیز شیمیایی در این مرحله است که خواص شیمیایی و فیزیکی کلاف های گرم را تعیین
می کند.
نحوه انجام فرآیند احیا
در کوره قوس الکتریکی به صورتی است که با استفاده از جریان بالا که توسط الکترود
ها و لوله های خنک کننده به مواد مذاب داخل کوره منتقل می شود، ناخالصی های مواد
قراضه و آهن اسفنجی جدا شده و حاصل آن فولاد مذاب آهنی بدون هیچگونه ناخالصی است.
نام دیگر این روش، میدرکس نیز می باشد که در کارخانه فولاد مبارکه اصفهان مورد
استفاده قرار می گیرد.
گرما دهی خارجی کوره قوس
الکتریکی، نسبت به فرآیند اکسیژن پایه که حرارت دهی آن توسط اکسیداسیون گرمازای
عناصر درون شارژ کوره انجام می شود، کنترل حرارت بیشتری داشته و از این رو مقادیر
عناصر آلیاژی که در این روش اضافه می شوند، بیشتر است. البته بهتر است بدانید
تولید فولاد در این روش، اکسید کننده نیست و اختلاط سرباره کوره قوس الکتریکی و
فلز به شدت روش اکسیژن پایه نیست؛ به هیمن علت درصد کربن در این روش بیشتر از
005/0 درصد است.
تفاوت های کوره القایی و کوره قوس الکتریکی
در ادامه به بررسی تفاوت
این دو روش برای تولید فولاد مذاب پرداخته ایم:
تمایز در حرارت دهی
از نظر حرارت دهی، کوره
القایی سریع تر عمل می کند؛ زیرا حرارت درون شارژ کوره تولید شده و پس از ذوب
حرارت قوس از طریق سرباره به فولاد منتقل می شود. همچنین این کوره ها شبیه به یک
حوضچه هستند و بخش زیادی از گرما در قوس الکتریکی از طریق محافظ و دیواره ها هدر
می رود.
ظرفیت حذف سولفور
ظرفیت حذف سولفور، فسفر
و اکسیدزدایی در کوره قوس از القایی بیشتر بوده و سرباره در روش القایی سرد می
باشد. این در صورتی است که سرباره در کوره قوس گرم بوده و مقدار نیتروژن نیز در
این روش بیشتر است. با این وجود می توان گفت سبب کاهش انتشار دی اکسید کربن شده و
در نتیجه آسیب های زیست محیطی در روش قوس کمتر می باشد. لازم به ذکر است تولید
فولاد به روش کوره القایی اتلاف گاز، پسماند، سر و صدا و مصرف انرژی بیشتری دارد.
نرخ بازیابی عناصر
آلیاژی
کوره القایی از نظر نرخ
بازیابی عناصر آلیاژی ذوب شده، هم زن الکترومغناطیسی، ذوب، کنترل دما و شدت هم زدن
بر کوره قوس الکتریکی برتری دارد. با این وجود می توان گفت کیفیت فولاد در این روش
بهتر بوده و در نتیجه نرخ فولاد سبب اثرگذاری در هزینه تولید ورق ها و مقاطع
فولادی مانند قیمت ورق آهن روغنی، سیاه و ... خواهد شد. امروزه این فلزات کاربردهای
بسیاری را در صنعت به خود اختصاص می دهند. به طور مثال اصلی ترین کاربردهای
محصولات سرد یا روغنی در صنعت خودروسازی، لوازم خانگی، تولید فولاد گالوانیزه، ساخت
وسایل آشپزخانه، مبلمان و ... است. با این وجود روش احیا و تولید فولاد خام، بر
نرخ این فلز و در نتیجه سایر مقاطعی که از این طریق تولید می شوند، مؤثر است.
تفاوت در سایز
از نظر ابعاد کوره باید
گفت کوره های القایی کوچک تر بوده و برای شرکت های فولادسازی کوچک تر مناسب هستند؛
در نتیجه ظرفیت و بازدهی تولیدی کوره های قوس الکتریکی بیشتر بوده؛ زیرا ابعاد
بزرگ تری دارد.
توانایی تصفیه
تفاوت در سرباره گرم و
سرد، یکی دیگر از تفاوت های کوره القایی و قوس الکتریکی است. کوره القایی سرباره
سرد و کوره قوس سرباره گرم دارد. همچنین از نظر حذف فسفر، گوگرد و اکسیداسیون کوره
قوس برتری داشته و نیتروژن و کلر بیشتری نیز تولید می کند.
تصفیه مقدار کربن
کوره های القایی به اصل
گرمایش القایی فولاد خام را تولید می کنند؛ در صورتی که کوره های قوس، برای ذوب
نیاز به الکترود دارند.
بازده ترمودینامیکی
و جنبشی
عمل همزن الکترومغناطیسی در کوره های القایی سبب بهبود بخشیدن شرایط جنبشی واکنش، همگن سازی درجه حرارت و ترکیب فولاد مذاب می شود.
حتما بخوانید:تفاوت کوره های میدرکس
بهره وری
از نظر زمان تولید فولاد
مذاب، باید گفت کوره های قوس الکتریکی به علت ورود انرژی شیمیایی، اکسیژن و کربن
در زمان کمتری فولاد را تولید می کند. این زمان در حدود 50 تا 60 دقیقه است. در
مقابل تولید فولاد در کوره های القایی 120 تا 150 ساعت است؛ در نتیجه فرآیند تولید
زمان بیشتری نیاز داشته و در نهایت عرضه محصولات و مقاطع فولادی دیرتر انجام می
گردد.
این موضوع برای شرکت ها
و کارخانجاتی که نیاز به تولید محصولات فولادی در تناژ بالا دارند، بسیار حائز
اهمیت است؛ زیرا سبب ایجاد وقفه در تولید و در عرضه و فروش خواهد شد. شرکت فولاد
مبارکه نیز برای تولید محصولات خود از روش قوس استفاده می کند؛ از این رو انواع
مختلف ورق های فولادی را با بهترین کیفیت از نظر پوشش سطح، خواص و کاربری عرضه می
کند.
یکی از جذاب ترین فلزاتی که توسط این شرکت تولید می شود، ورق گالوانیزه است که از طریق پوشش دهی ورق های روغنی یا اسیدشویی تولید شده و مقاومت آن در برابر عوامل زنگ زدگی و خوردگی سبب استفاده در صنایع مختلف به خصوص ساختمان سازی شده است. قیمت ورق گالوانیزه کیلویی نیز بسته به نرخ پایه این شرکت در بورس کالا یا بازار آزاد تعیین شده و بسته به میزان پوشش رنگ، کیفیت فولاد پایه، نوسانات ارز، شرکت تولید کننده و کیفیت پوشش روی در آن متفاوت است. تولید ورق های رنگی شیروانی و فرمینگ از اصلی ترین کاربردهای این فلزات است. برای کسب اطلاعات بیشتر و خرید هر محصول می توانید با کارشناسان شرکت آهن اینفو تماس حاصل فرمایید.
جمع بندی
در این مقاله به بررسی
تفاوت کوره القایی و قوس الکتریکی پرداخته شد که هر دو در جهت احیا سنگ آهن
استخراج شده از معادن و تولید آهن و فولاد خام مورد استفاده قرار می گیرند. البته
لازم به ذکر است امروزه بیشترین تولید فولاد خام به وسیله روش کوره بلند انجام می
گیرد که هزینه و زمان بسیار زیادی را نیاز دارد. در کشور ما به طور معمول از روش
میدرکس یا همان به کارگیری کوره های قوس الکتریکی استفاده می کنند.
اصلی ترین تفاوت این دو
روش در میزان کربن برآورد شده است؛ زیرا در روش القایی، در ذوب مواد از جریان القا
استفاده می کنند که درصد کربن را افزایش نمی دهد. در صورتی که شیوه قوس الکتریکی
همراه با ذوب مواد با استفاده از الکترود گرافیت انجام می گیرد؛ بنابراین الکترودی
که به کار رفته است، منجر به افزایش کربن می شود.
با این وجود هر دو روش
مزیت های خاص خود را دارند. به طور مثال کوره های القایی سرعت بالایی در تولید
داشته و ذوب بسیار تمیزی را به همراه دارند. همچنین در مصرف مواد صرفه جویی می
کنند. کوره های قوس نیز با ایجاد قوس بین الکترودها، قراضه های آهن به همراه آهن
اسفنجی و مواد سرباره منجر به جدا شدن ناخالصی های مواد و به وجود آمدن خواص
الکتروشیمیایی در آن ها خواهند شد. جالب است بدانید امروزه حدود 1 چهارم فولاد در
جهان به وسیله این روش تولید می گردد. در نهایت نیز به سرعت تولید دو فرآیند اشاره
شد و به این نتیجه رسیدیم که کوره های قوس الکتریکی انرژی شیمیایی بیشتری داشته و
از این رو اکسیژن و کربن را با سرعت بیشتری تولید می کنند. در صورتی که تولید
فولاد در کوره های القایی حدود 120 تا 150 دقیقه به طول می انجامد.