گندله چیست؟
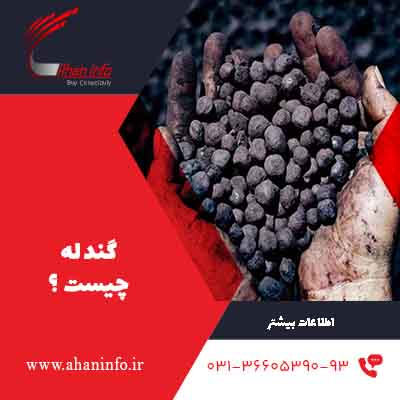
در فرآیند تولید ورق های فولادی، ماده اولیه
برای تولید آهن و فولاد خام، گندله pellet iron ore نامیده می شود که شامل عناصری در ترکیبات خود از
جمله آهن در حدود بیشتر از 63 درصد است. شکل ظاهری این ماده شبیه به گلوله های
کوچک ریز و درشت بوده و از کنسانتره سنگ آهن استخراج شده از معدن تولید می شود.
پیش از بررسی گندله باید به بررسی فرآیند
آگلومراسیون (Agglomeration) بپردازیم که یکی از مهم ترین پروسه ها در استخراج
سنگ آهن و تولید گندله است. در این فرآیند ذراتی با اندازه بزرگ از سایز
های کوچک تر ساخته می شوند. این فرآیند معمولاً در صنایع متالوژی، فولادسازی،
شیمیایی و داروسازی مورد استفاده قرار می گیرد.
در تولید آهن خام نیز کانه های دانه ریز آهن
قابل استفاده نمی باشند؛ زیرا میزان تراوایی گاز را در روش کوره بلند به شکل
نادرستی کم کرده و سبب ایجاد اختلال در عملکرد کوره خواهند شد، از این رو باید به
گندله تبدیل شوند. در ادامه سایر مشخصات گندله از جمله تاریخچه به وجود آمدن آن در
صنعت فولاد شرح داده شده اند تا بتوانید درک بهتری از چرخه فولادسازی و چالش های
این صنعت داشته باشید.
تاریخچه
گندله سازی
تاریخچه آغاز تولید گندله توسط یک دانشمند
سوئدی با نام ا.ج اندرسون در سال 1912 انجام شد، اما نام گندله برگرفته از کشور آمریکا
و به پس از پایان جنگ جهانی دوم باز می گردد. اولین کارخانه گندله سازی نیز در
مینسوتا و سال 1955 فعالیت خود را آغاز کرد و پس از آن در ابتدا دهه 80 میلادی، 50
درصد از کوره های بلند در کشورهای آمریکا، کانادا و مکزیک، از گندله استفاده می
کردند.
به طور معمول در گذشته پودرهایی که از طریق
استخراج سنگ آهن تولید می شدند، زائد تلفی شده و مورد استفاده قرار نمی گرفتند،
اما پس از گذشت زمان و با تولید گندله، امروزه این مواد به عنوان ماده اولیه تولید
آهن خام و یکی از مهم ترین محصولات کوره های احیا مستقیم و بلند شناخته می شوند.
از ویژگی گندله ها می توان به تخلخل بالا،
استحکام و مقاومت قابل توجه در ترکیبات شیمیایی خاص و افزایش کارایی و کیفیت در
آهن خام تولیدی اشاره کرد. استفاده از این ماده تا حدی سبب کاهش قیمت آهن آلات نیز
خواهد شد و این موضوع در نهایت به مناسب بودن نرخ ورق ها و مقاطع فولادی منجر می
شود.
فرآیند
تولید گندله
در واقع گندله سازی فرآیندی است که به وسیله
غلتاندن ذرات ریز سنگ آهن انجام می شود و در آن مواد چسباننده جهت افزایش پیوند و
تخلخل محصولات نهایی با استفاده از دستگاه گندله سازی استوانه ای یا دیسکی به این
ذرات اضافه می شوند. بنابراین می توان گفت گندله خام (Green Ball) به وسیله پروسه سخت شدن، خشک سازی، پیش گرم کردن،
گرم کردن در دمای 1350 درجه و سپس سرد کردن تولید می شود. دو روش برای ساخت گندله
وجود دارد که هر کدام مراحل
خاصی دارد. در ادامه به شرح اختصاری هر روش می پردازیم:
روش مخروطی
با این حال مراحل کلی تولید گندله آهن به
روش مخروطی و به دست آمدن این فلزات به شرح زیر است:
- تهیه مواد اولیه
ابتدا مواد اضافی ذکر شده در فوق، به سنگ
آهن دارای خلوص 5/67 درصد که به صورت پودر در آمده، افزوده می شوند تا علاوه بر
ایجاد تخلخل در گندله ها، پیوند عناصر این ماده را با یک دیگر ایجاد کنند. این
عملیات به وسیله مخلوط آن ها در پلت ساز که سنگ معدن و مواد افزودنی نیز در آن
قرار داده می شوند، صورت می گیرد و سبب تنظیم ترکیبات شیمیایی و خواص متالورژیک
گلوله ها خواهد شد.
- استفاده از مخروط گندله سازی
سپس برای تولید گلوله های گندله، از دیسک
هایی در مقیاس صنعتی استفاده می شود که قادر هستند با استفاده از پاشش
آب، رطوبت مورد نظر برای تولید را ایجاد کنند.
- پختن گندله خام
در مرحله بعدی، گندله خام پخته می شود تا
برای قرار گیری در کوره مقاومت کافی را داشته باشد و خرد نشود. محصول نهایی طی این
مرحله گندله سبز نامیده می شود.
- خشک کردن گندله سبز
در این قسمت رطوبت گندله سبز خشک شده و از
بین می رود.
- پیش گرم کردن
سپس گندله ها در دمای 1000 درجه سانتی گراد
در جهت پیش گرم شدن قرار می گیرند.
- پخت گندله
در مرحله آخر مجدداً گندله ها تحت دمای 50 درجه سانتی گراد پخته شده تا از ایجاد ترک و خرد شدن آن ها جلوگیری شود و همچنین مقاومت آن ها را افزایش دهند. در نهایت نیز آنالیز شیمیایی این ماده در کیفیت ورق های فولادی که به وسیله آهن خام به دست آمده از گندله تولید می گردند، تأثیر دارد. همین موضوع سبب تفاوت قیمت ورق فولادی با یک دیگر خواهد شد. به طور مثال عنصر کربن و منگنز در ورق سیاه نسبت به ورق سرد یا روغنی بیشتر دیده می شوند و از این رو، مقاومت ورق گرم یا سیاه نیز بیشتر است.
حتما بخوانید:تفاوت آهن و چدن
روش دیسکی
در این روش ابتدا باید گلوله های سنگ آهن،
پیکربندی شوند که این پروسه سبب جریان یافتن هوا بین گلوله ها شده و علاوه بر آن
مقاومت در برابر هوای ذوب را که به وسیاه لایه های مواد به بالا جریان پیدا می
کنند، کاهش می دهد. به همین علت است که استفاده از سنگ آهن به صورت گلوله ای و به
جای ذرات ریزتر ترجیح داده می شود. کیفیت این گلوله ها نیز به عوامل مختلفی وابسته
است که از جمله آن ها می توان به اندازه، مقدار آب مصرفی، سرعت چرخش دیسک، زمان
مکث، کیفیت و کمیت چسب (های) استفاده شده و زاویه شیب دیسک اشاره کرد.
در ادامه فرآیند، نرمه سنگ آهن در ابعاد 45
میکرون به همراه آب و سایر مواد چسباننده مانند آهک و شیره آن، هیدرواکسید کلسیم،
بنتونیت و و انواع چسبهای آلی و معدنی با یک نسبت مشخص در دیسک گندله سازی به
صورت دورانی حرکت کرده و ترکیب می شوند تا گندله تولید شود. در مورد آنالیز
شیمیایی این ماده نیز می توان گفت درون ترکیبات آن عناصری مانند منگنز، کلسیم، تیتانیوم، آلومینیوم، منیزیم، سیلسیم،
وانادیوم، گوگرد و فسفر وجود دارد.
انواع
گندله
به صورت کلی گندله بر اساس
ابعاد و سایز و همچنین میزان تخلخل به انواع مختلفی تقسیم بندی می شود؛ از این رو
ابتدایی ترین آن ها گندله بزرگ نامیده شده که قطری بین 20 تا 30 میلی متر دارد.
این محصول بیشترین کاربرد را در تولید محصولات فولادی و مصالح ساختمانی مانند
سیمان به خود اختصاص می دهد.
گندله عادی دارای قطر 10 تا
15 میلی متر بوده و بیشتر برای احیا مستقیم در کوره های بلند از آن استفاده می
شود. از سوی دیگر گندله ریز از کوچک ترین نوع می باشد و قطر 3 تا 8 میلی متری
دارد؛ از این رو برای ساخت کلوخه کاربرد دارد. و در آخر می توان به گندله اسفنجی
اشاره کرد که ساختار کروی شکل داشته و در کارخانجات فولاد سازی به جای آهن قراضه و
در فرآیند ریخته گری کاربرد دارد. نام دیگر این محصول نیز آهن اسفنجی می باشد.
مشخصات
گندله
همان طور که اشاره شد برای تولید گندله از
کنسانتره سنگ آهن استفاده می شود. فرآیند آگلومراسیون نیز شامل سه بخش سینترینگ یا
کلوخه سازی(Sintering) ، گندله سازی (Pelleting) و بریکت سازی (Briquetting) است. کنسانتره سنگ آهن نیز از طریق از بین بردن ناخالصی های آهن و افزایش
عیار آن با خرد کردن و نرم کردن تولید می شود. اندازه این مواد باید کمتر از 45
میکرون باشد. برای ساخت آن نیز از مواد افزودنی با قابلیت چسبانندگی مانند
بنتونیت، شیره آهک، مواد آلی، آهک، سیمان و آب نیز استفاده می شود.
این مواد علاوه بر داشتن خاصیت چسبانندگی و
ایجاد پیوند بین مواد، سبب بهبود خواص مکانیکی و فیزیکی آن ها خواهند شد. همچنین
سبب ایجاد سرباره، تسهیل فرآیند افزایش تخلخل و استحکام و در نتیجه بهبود احیا
پذیری در روش کوره بلند یا احیا مستقیم خواهند شد.
گندله آهن تولید شده نیز در ابتدا خام بوده
و هر گلوله اندازه ای بین 6 تا 16 میلی متر میلی متر دارد. برای احیا گندله از روش
های کوره بلند یا احیا مستقیم استفاده می شود. این مواد معمولاً دارای 64 تا 72
درصد آهن و عناصر مختلف دیگری هستند که سبب به وجود آمدن خواص مختلف در آن ها می
شوند. در ادامه مشخصات ساختاری گندله در قالب جدول برای شما آورده شده است:
مزایای
استفاده از گندله
گندله از مزیت های بسیاری
برخوردار می باشد و همین موضوع سبب شده تا به عنوان یکی از اصلی ترین مواد اولیه
فولادسازی در کارخانجات مختلف از آن استفاده کنند. این مزیت ها شامل موارد زیر
هستند:
- استحکام مکانیکی بالا
- پایداری حرارتی و مقاومت در برابر شرایط دمایی و
فشارهای بالا
- آهن خالص بالاتر و وجود ناخالصی کمتر نسبت به سایر
مواد اولیه
- کاهش مصرف انرژی در زمان تولید
- افزایش بهره وری تولید به وسیله کوره های بلند
- کمتر شدن انتشار گازهای گلخانه ای و کاهش آلودگی هوا
- پایداری مناسب و جلوگیری از شکنندگی به خصوص در صورت
استفاده از گندله های درشت تر
- کاهش هزینه های حمل و نقل به سبب سبک بودن گندله ها
- افزایش کارآیی روشهای مختلف احیای اکسید آهن و کوره بلند
- کاهش میزان سرباره تولیدی به ازای هر تن تولید آهن
- نگهداری آسان
کاربرد
گندله
همان طور که اشاره شد، مهم ترین کاربرد
گندله آهن، در ساخت فولاد و محصولات حاصل از آن است. همان طور که می دانید فولاد
خام در برابر عوامل رطوبتی و خوردگی ضعیف است؛ در نتیجه با استفاده از فرآیند
گالوانیزاسیون لایه ای از جنس فلز روی بر سطح آن اعمال می کنند تا ورق گالوانیزه
به دست آید.
این محصول مقاومت بالایی در برابر رطوبت،
زنگ زدگی، خوردگی و اکسیداسیون دارد، اما جالب است بدانید نرخ خرید ورق گالوانیزه با وجود داشتن این ویژگی ها و سایر مشخصاتی مانند
قابلیت رنگ پذیری، فرم پذیری و جوش پذیری مقرون به صرفه به شمار می آید و از این
رو کاربردهای بسیاری را به خود اختصاص می دهد. دیگر کاربردهای گندله عبارت اند از:
صنایع ساختمانی برای ساخت
سیمان: استفاده از گندله سبب شده تا ویژگی های اصلی سیمان به عنوان مهم ترین
متریال ساختمانی یعنی مقاومت فشاری و کششی بهبود یافته و این موضوع در نهایت سبب
افزایش کارایی فرآیند تولید و کاهش هزینه تولید کمک می کند.
- فولادسازی
- ساخت بریکت و آهن اسفنجی
- تولید فولاد خام
- کلوخه سازی
- فرآیند احیا مستقیم
- جایگزین مناسب به جای آهن قراضه
حتما بخوانید:تفاوت آهن اسفنجی و گندله
انواع
دستگاه های گندله سازی
انواع دستگاههای گندله سازی شامل موارد زیر
می باشند:
- دیسک گندله ساز
- دیگواره گندله ساز
- کوره پخت
لازم به ذکر است، گندله که برای روش احیا
مستقیم مورد استفاده قرار می گیرد، با روش کوره بلند متفاوت بوده و باید درصد آهن
بیشتر و در نتیجه ناخالصی کمتری را در ترکیبات خود داشته باشد. گندله های کوره
بلند باید قطر بیشتر و استحکام بالاتری را نیز به خود اختصاص دهد. همچنین در زمان
احیا پذیری آهن، مواردی مانند سطح، ماده، تماس مواد جامد و گاز و درجه تخلخل در
کیفیت نهایی آن اثرگذار هستند. روش تولید نیز نقش مهمی در این فرآیند قیمت گذاری
دارد، اما مهم ترین نکته، میزان بهره مندی یک کشور از معادن سنگ آهن و کارایی آن
می باشد.
کارخانه
های تولیدکننده گندله در ایران
جالب است بدانید ایران یکی از تولید کنندگان
برتر گندله در جهان به شمار می آید و تحقیقات در این زمینه نشان دهنده این است که
در سال 1399 بیش از 46 میلیون تن گندله در کشور تولید شده و نسبت به سال قبل 10
درصد افزایش یافته است. در بین تولید کنندگان نیز ابتدا گل گهر با تولید 2/12
میلیون تن در رتبه اول و سپس فولاد مبارکه اصفهان با تولید 3/7 میلیون تن در رتبه
دوم قرار دارد. میدکو با تولید 6.2 میلیون تن و فولاد خوزستان با 5.5 میلیون تن در
رده های سوم و چهارم قرار دارند.
در این بین می توان گفت کارخانه فولاد
مبارکه یکی از تولید کنندگان برتر ورق های فولادی در کشور شناخته می شود و انواع
ورق سیاه، روغنی، اسیدشویی، گالوانیزه، رنگی و شیروانی و قلع اندود را با بهترین
کیفیت تولید و عرضه می کند.
همچنین یکی از اصلی ترین کاربردهای ورق
گالوانیزه تولید شده در این کارخانه برای ساخت محصولات فرمینگ و شیروانی است که در
صنعت ساختمان سازی برای پوشش دهی انواع سقف های داخلی و خارجی به کار برده می
شوند؛ در نتیجه می توان گفت یکی از مهم ترین عوامل در برآورده هزینه ساخت و ساز، قیمت ورق شیروانی است که با داشتن فرم ها و رنگ های مختلف در موارد مختلف پوشش سقف و دیوار
انواع مکان ها به کار برده می شود.
جمع
بندی
همان طور که در مطلب اشاره
شد، برای تولید آهن، فولاد و آلیاژهای آن ها نیاز به یک ماده کروی شکل به نام
گندله داریم. این ماده در ترکیبات خود دارای بیشتر از 63 درصد آهن می باشد. گندله در قالب گلوله های بسیار ریز
مورد استفاده قرار می گیرد و ماده اولیه برای تولید آن کنسانتره به دست آمده از
سنگ آهن است. برای ساخت این ماده روش های مختلفی وجود دارد، اما دستگاه های آن
شامل دیسک های گندله ساز، دیگواره و کوره پخت می باشند.
از گندله در روش کوره بلند و
احیا مستقیم در جهت فراوری سنگ آهن و حذف ناخالصی های آن استفاده می کنند. البته
بهتر است بدانید گندله ای که در هر کدام از این روش ها به کار برده می شود با
دیگری متفاوت است؛ زیرا گندله مورد استفاده در روش احیا باید درصد بیشتری از آهن و
ناخالصی کمتری داشته باشد.
از مزیت های گندله که برای
فراوری سنگ آهن کاربرد دارد می توان به استحکام و مقاومت قابل قبول، تخلخل بالا،
افزایش کارایی و کیفیت در آهن خام تولیدی اشاره کرد. این مزایا سبب شده تا فولاد
مذاب با درصد خلوص آهن بیشتری تولید شود و در نتیجه محصولات فولادی از جمله انواع
ورق سیاه، اسیدشویی، روغنی و پوشش دار از کیفیت قابل قبولی برخوردار باشند.